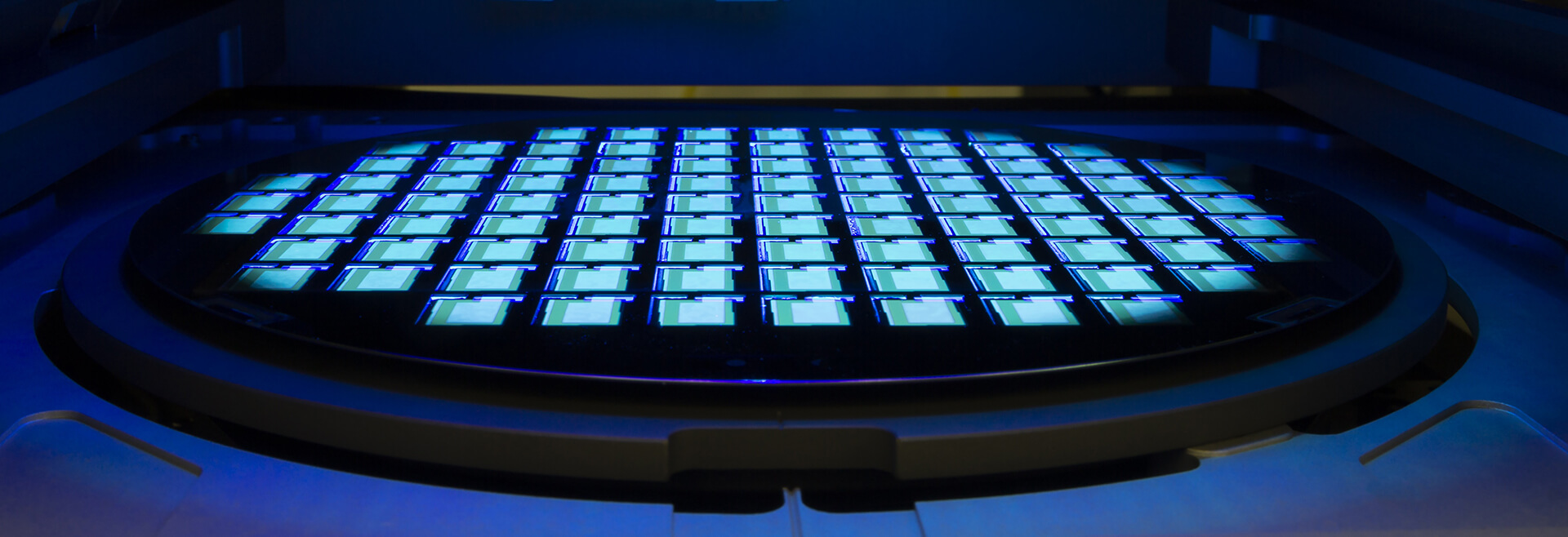
Cleaning Systems—Post CMP Clean
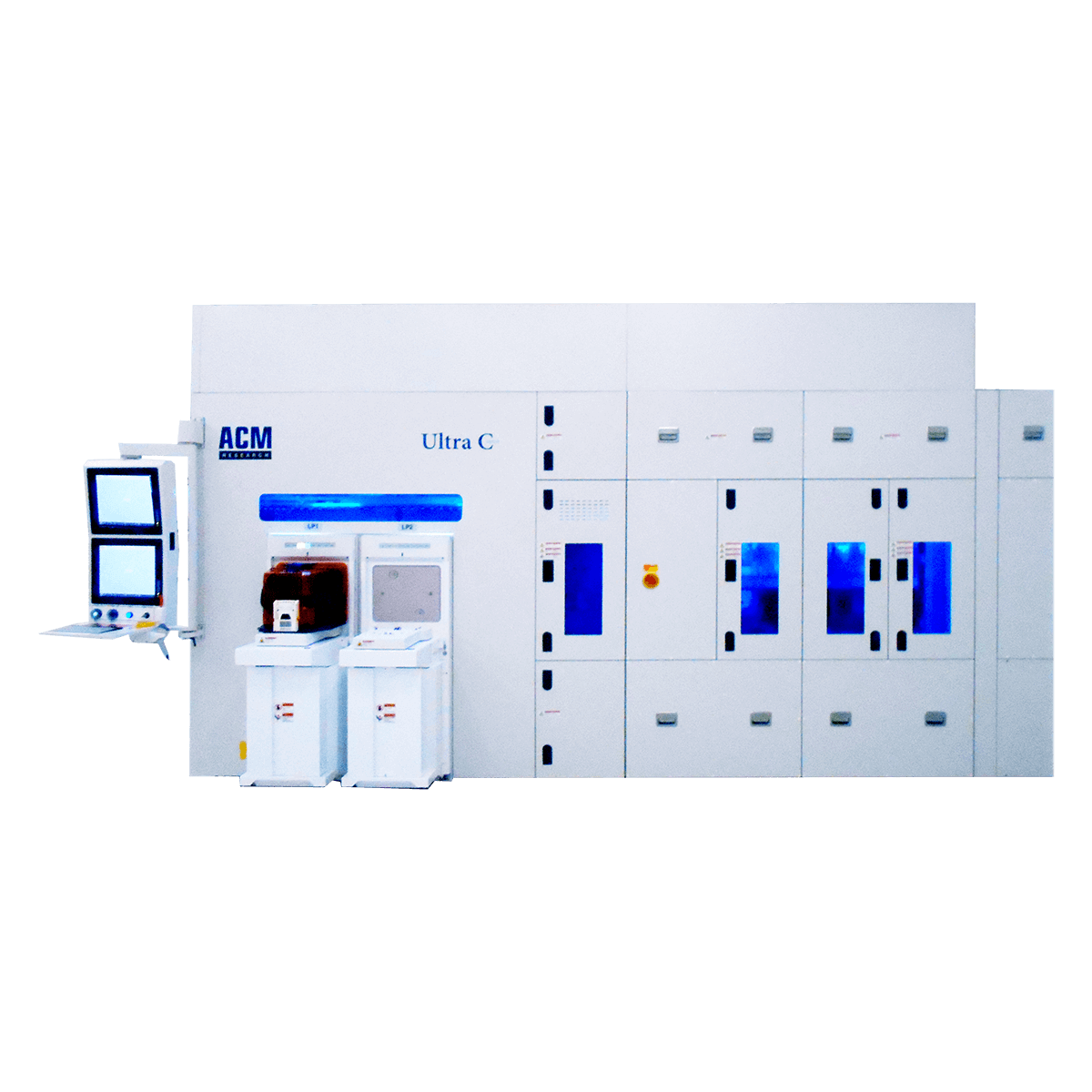
Meet emerging requirements for post-CMP cleaning
Post-CMP cleaning has a critical role in meeting stringent CMP defects for device reliability and yield requirements. It is used to reduce particles, organic residues, and metallic contaminants from wafers without damaging the wafer surface and serves as a cleaning step following the CMP process used to manufacture high quality silicon (Si) and silicon carbide (SiC) substrates. In particular, SiC wafers require particular care with respect to their processing and handling due to their innate thinness, brittleness, and tendency toward surface inconsistencies, and our Post-CMP cleaning tool is optimized to clean these sensitive substrates.
Our Ultra C post-CMP tool builds on our existing proven technology – including our Smart Megasonix technology – to meet emerging requirements for this application. The tool is equipped with a doubled-sided brushing and clean step that ensures removal of all slurry and SiC residues after wafer polishing. In our wet-in dry-out (WIDO) pre-clean configuration, wafers are kept wet after the brush step, then moved to either two or four clean chambers and are processed using up to three chemicals, with a rinse in between each chemical, rinsed again with DI water, and then exposed to a nitrogen (N2) spin dry. The resulting wafers exhibit superior particle performance.
The Ultra C post-CMP tool is also available in two additional configurations:
- An offline wet-in dry-out (WIDO) pre-clean tool, where wet wafers are transferred from the CMP tool to a DI water bath, and then manually moved to the WIDO offline tool. This option offers the same particle performance as the online WIDO configuration while saving valuable fab floor space.
- If you are manufacturing silicon wafers using a CMP platform with a built-in cleaning chamber and during capability, you need our dry-in dry-out (DIDO) option. In this configuration, wafers are manually transferred to the pre-clean tool via the loadport, then processed the same as with the WIDO pre-clean tool.
Major Benefits
- Available in 6- and 8- inch configurations for silicon carbide (SiC), and 8- and 12- inch configurations for silicon (Si) wafer manufacturing.
- Offers wet-in dry-out (WIDO) and dry-in dry out (DIDO) configurations, with 2-, 4- and 6-chamber options.
Features and Specifications
- Multiple configurations for Si and SiC wafer manufacturing
- Two brush chambers and two to four clean chambers
- Nitrogen dry and spin
- Particle performance of <15 particles at or above 37nm and 20-25 particles greater than 28nm
- Metallic contamination of ≦ 1E+8 (atoms/cm2)
- WIDO throughput up to 35 WPH (4-chamber tool)
- DIDO throughput up to 60 WPH
- SAPS™ Megasonix
Contact Us
Looking for customized solutions for your wet wafer processing, ECP, Furnace, Track and SFP?