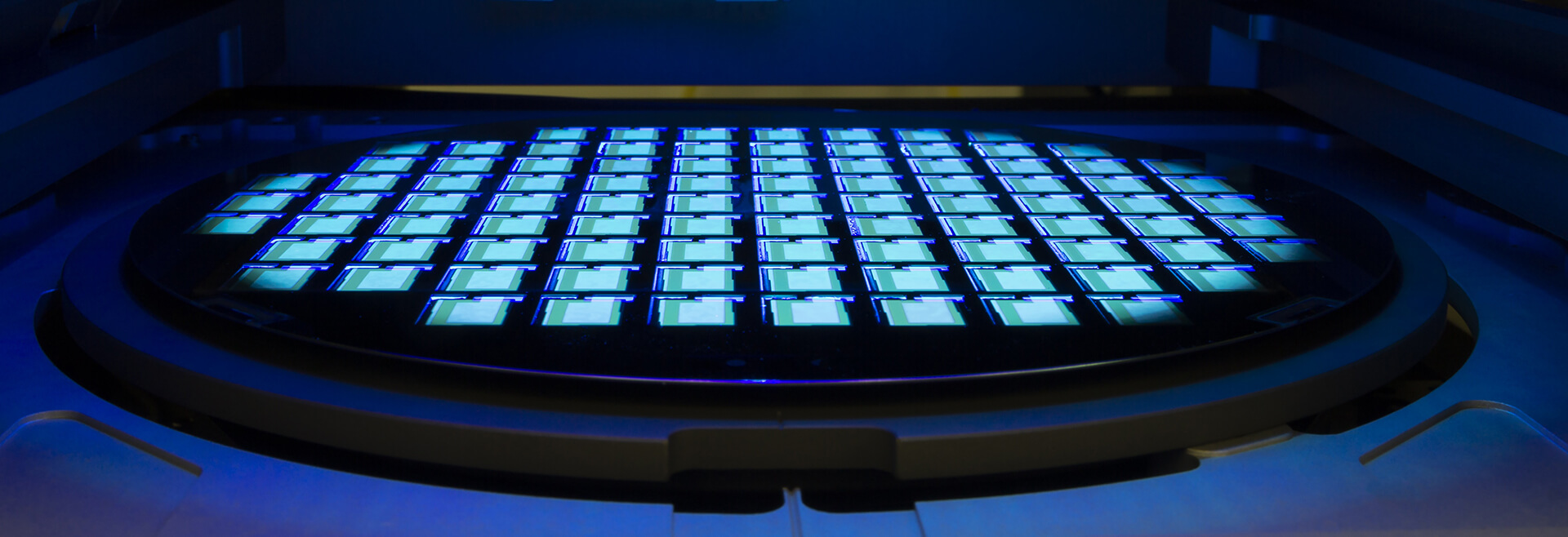
Cleaning Systems—Ultra C Tahoe
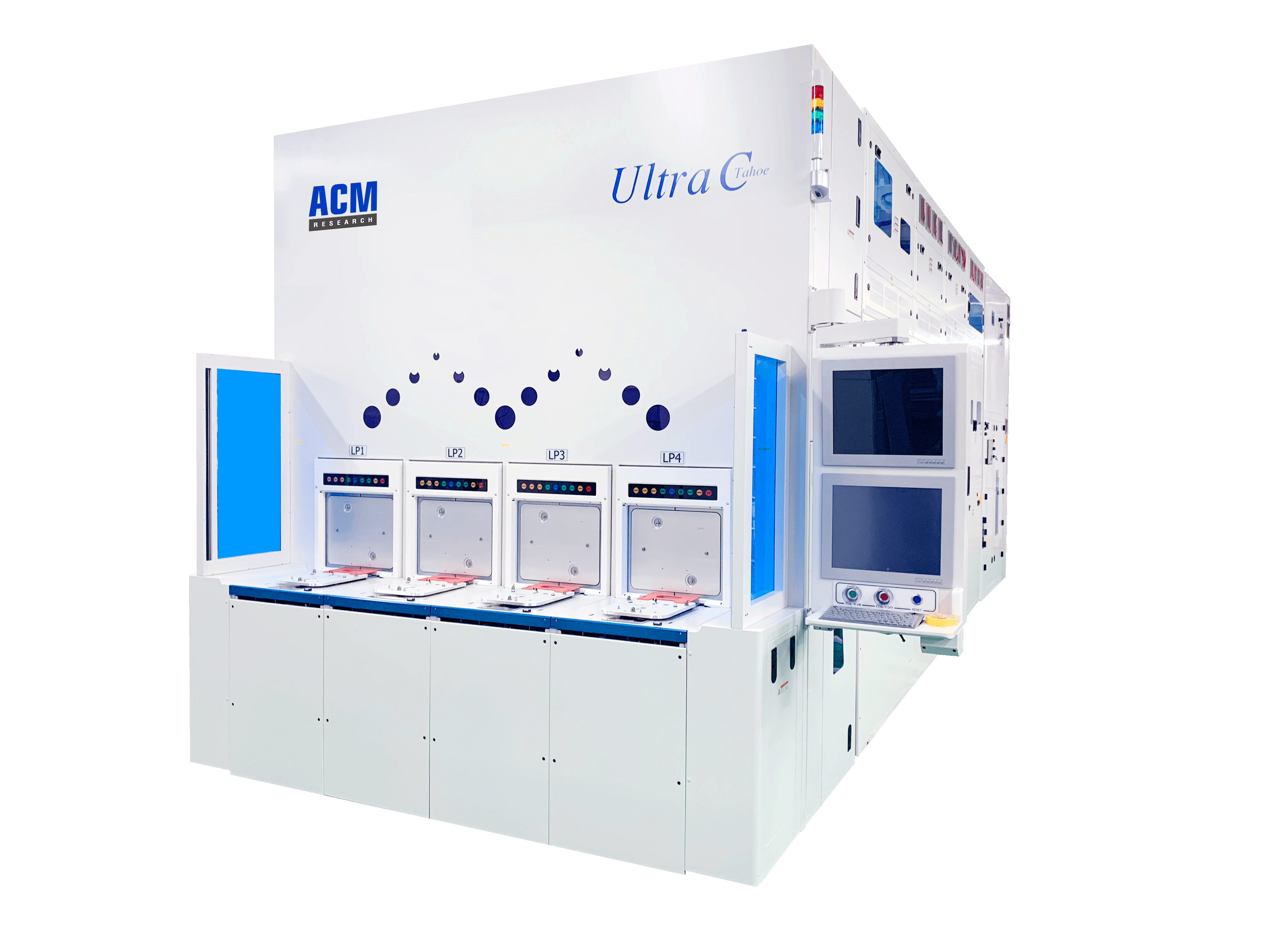
For advanced technology node SPM cleaning processes
ACM Research’s Ultra C Tahoe advanced cleaning tool meets the demanding technical requirements of advanced nodes for foundry, logic and memory applications. The tool delivers the performance of standalone single-wafer cleaning tools on low-to-medium temperature sulfuric peroxide mix (SPM) processes. Tahoe’s patented hybrid architecture is among the first in the industry to combine batch wafer processing and single wafer cleaning chambers into the same SPM tool. The hybrid architecture delivers enhanced cleaning performance, high throughput, and process flexibility, with up to 75% reduction in chemical consumption.
High-performance, eco-friendly SPM cleaning technology
“Ultra C” stands for “ultra-clean”—and with the Ultra C Tahoe cleaning system, this means both to the processes the tool performs, as well as its impact on the environment.
The Ultra C Tahoe system takes sulfuric peroxide mix (SPM) cleaning to the next level by reducing the amount of sulfuric acid needed for the process, which in turn lowers both chemical and post-process waste treatment costs. This drives an estimated cost savings of up to $500,000 per year from sulfuric acid alone, with additional environmental and cost benefits from reduced sulfuric acid treatment and disposal.
Tahoe is the better choice for advanced node applications
Conventional SPM cleaning is performed in a wet bench tool using sulfuric acid (H2SO4) and hydrogen peroxide (H2O2) to remove unwanted materials from silicon wafers during photoresist strip, post-etch clean, post-implant clean and post CMP clean processes.
Today’s SPM bench tools cannot achieve the cleaning performance required for technology nodes below 28nm, leaving SPM single wafer processing as the only solution. However, the single wafer SPM process requires the SPM mixture to be heated to high temperatures, which calls for high chemical usage and releases sulfuric acid waste in the process, thereby harming the environment.
The Ultra C Tahoe mitigates these challenges using a two-step approach to optimize the advantages of wet bench and single wafer cleaning. First, the wafers are run through a batch cleaning step in the wet bench module, processed by SPM, and then go through quick dump rinsing (QDR). While still wet, the wafers are transferred to the single wafer module for further cleaning, using a standard RCA cleaning process or other process chemicals. The single wafer chamber is very flexible, and a hot isopropyl alcohol (IPA) vapor drying function can also be integrated for the patterned wafer drying process.
Ultra C Tahoe cleaning applications
The Tahoe is qualified for more than 30 production layers, including key loops such as lightly-doped drain (LDD) and source/drain (SD), with additional layers and applications in development. The Tahoe is the ideal solution for advanced node SPM cleaning applications, including:
- SPM photoresist stripping
- Post etch cleans
- Post IMP cleans
- Post CMP cleans
Major Benefits
Enhanced Particle Removal
The Tahoe platform’s advanced cleaning capabilities have achieved average particle counts of less than 6 particles at 26nm, meeting the stringent requirements for advanced node manufacturing. The tool is also capable of removing 1x nm particles for the most advanced logic and memory applications, with the addition of a smaller particle filtering system.
Higher Throughput
Featuring a 25-slot bench module and nine single-wafer chambers allows the system to deliver throughput exceeding 200 wafers per hour, comparable to the capacity of a 12-chamber SPM system.
Environmental and Cost Benefits
With a reduction of up to 75% in sulfuric acid consumption, the Ultra C Tahoe aligns with environmental regulations and sustainability goals, reducing costs for high-volume manufacturers.
Features & Specifications
- Low cross-contamination risk
- Excellent particle removal performance
- 300mm wafer compatibility
- Flexible chemical combinations are enabled by the single wafer module; platform accommodates up to four arms for dispensing up to three process chemicals
- Options include:
- Jet spray technology
- Patented SAPS/TEBO technologies
- Hot IPA drying
- Customizable to dispense:
- Standard clean (SC1)
- Hydrofluoric acid
- Ozonated deionized water (DI-O3)
- Other process chemicals
- Qualified on volume production lines
- Customized and configured to customer specifications
Contact Us
Looking for spare parts and customer support for your ACM Research Systems?