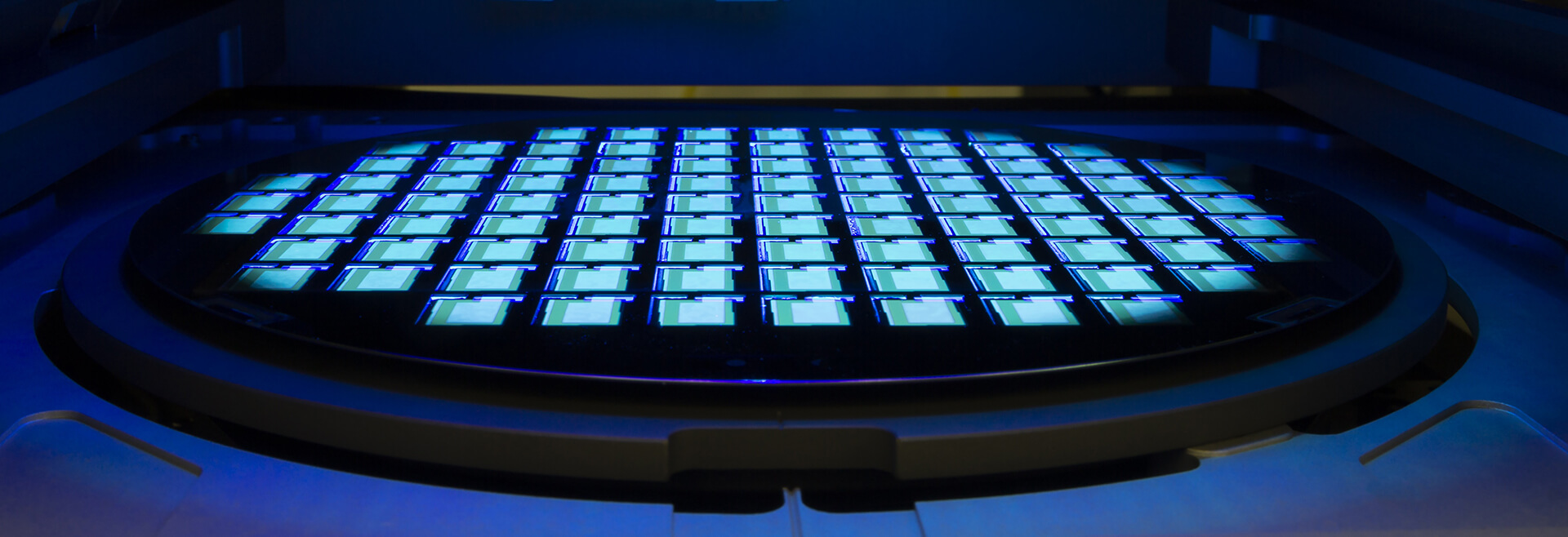
Developer Systems—Ultra C dv
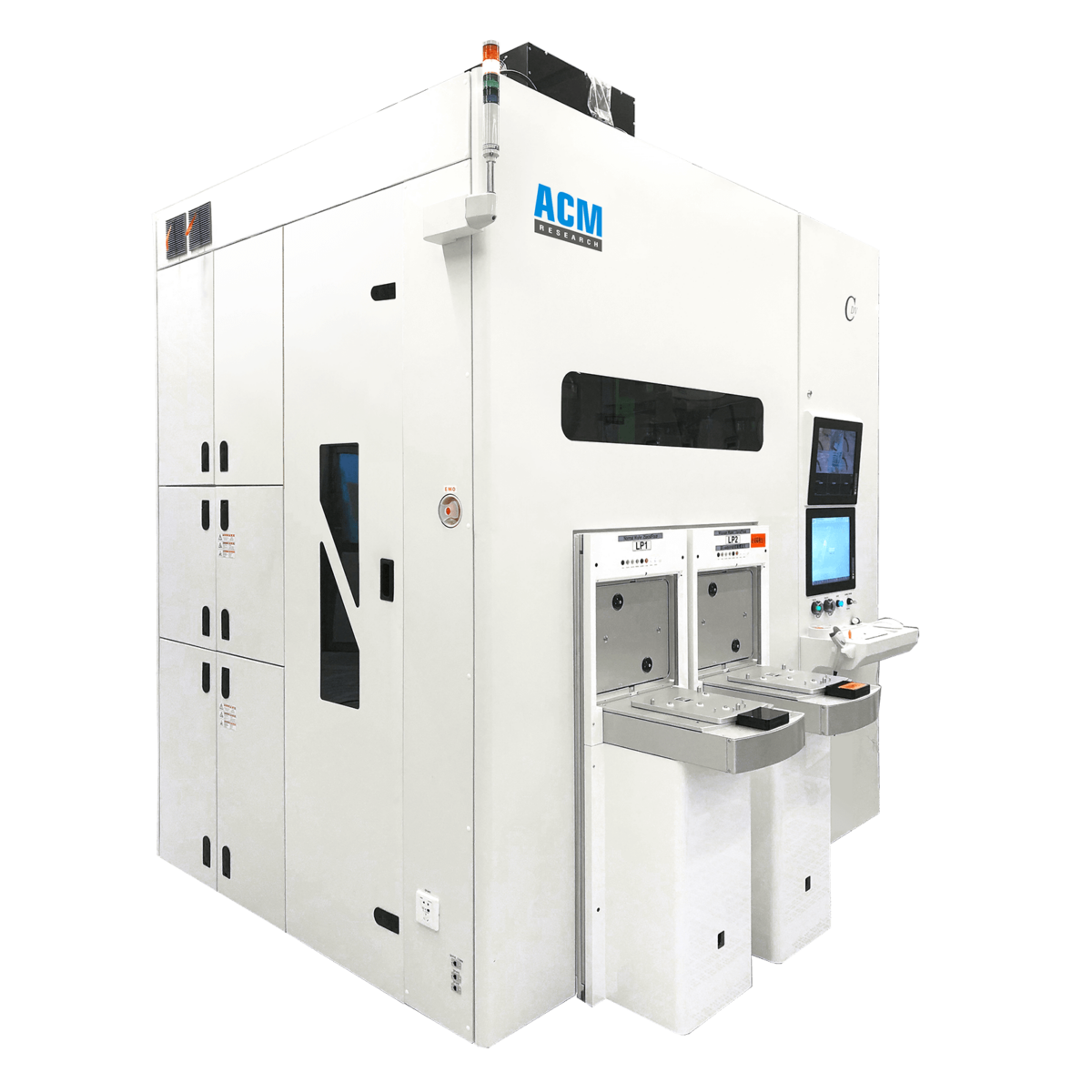
For wafer level packaging applications
Three photoresist development tools in one
The ACM Developer system performs crucial steps in the wafer level packaging (WLP) manufacturing process. This tool is compatible with 200mm and 300mm wafer processes, and is capable of performing the following steps in the lithography process:
- Post Exposure Baking (PEB)
- Developing
- Hard bake
With its superior technology, the Ultra C dv is designed to provide the precise flow rate and temperature control needed for quality photoresist development processes. A highly flexible tool, the ACM Developer provides more options and allows users to establish the best balance between throughput time and chemical cost usage through a choice of three different development methods.
Major Benefits
Three development methods in one tool
The Ultra C dv is capable of performing three different methods of wafer photoresist development: Spray, Puddle and Wet Spin. With its flexibility, it is very easy to switch between methods, and the tool can also be configured to perform a combination of all three methods.
Nozzle scan system
The nozzle scan system is designed to give users flexibility and control of their process. With programmable speed and movement range, the nozzle can be adjusted to suit the specific wafer thickness and process requirements.
Superior technology, ease of use
This system incorporates advanced component modules such as high-precision wafer transfer systems, superior fan filter & exhaust units, and independent control of the process environment for each chamber. All these modules are designed for ease of use while delivering the desired developer thickness and uniformity. Customizable software also allows the tool to be easily integrated into the production line.
Precise control
ACM tools contain state-of-the-art chemical temperature and flow rate control systems. This ensures that chemicals are released in exactly the correct amounts and temperatures throughout the manufacturing process. The Developer is able to provide a controlled flow rate that is +/- 0.3 LPM of the desired flow rate and +/- 0.5 celsius of the desired temperature.
Protecting the environment, reducing costs
Because the company is committed to protecting the world’s environment, all ACM systems are fitted with chemical recycle and filter systems that serve to reuse chemicals, decrease waste – and reduce the user’s costs.
Features & Specifications
- 8” and 12” wafer compatible
- Process module includes
- 1 to 4 sets of developing chambers with:
- ULPA FFU in each developing chamber
- 1 to 5 sets of liquid nozzles in each developing chamber
- N2 nozzle for wafer dry
- 1 to 3 backside cleaning nozzles
- 1 to 4 sets of developing chambers with:
- 2 to 14 hot plates
- 2 to 4 cold plate
- Chemical and plumbing module includes
- 1 to 5 sets of chemical delivery units for wafer developing and cleaning
- Wafer transfer module includes:
- 1 to 4 load port
- Optical wafer centering aligner
- Robot with 2 to 4 vacuum or mechanical arms
- ULPA FFU in robot bay
Contact Us
Looking for customized solutions for your wet wafer processing, ECP, Furnace, Track and SFP?